Durch das große Tor fällt Sonnenlicht in die Produktionshalle, Staub tanzt durch die Luft und legt sich auf die dunkle Arbeitsjacke von Thomas Schink. Strohballen stapeln sich bis unter die Decke, es rattert, zischt und surrt, die mehrteilige Maschinenkette läuft auf Hochtouren. Schink ist Prokurist und Qualitätsbeauftragter bei der Pahren Agrar GmbH mit Sitz in Zeulenroda- Triebes im Osten Thüringens. Doch am liebsten hält er sich im zwei Kilometer entfernten Läwitz auf. „Jeden Morgen führt mein erster Weg hierhin zu meinem Baby“, sagt Thomas Schink. Sein „Baby“ ist eine Hanfstrohaufschlussanlage, untergebracht in einer Arbeitshalle aus DDR-Zeiten. Mit Maschinen, die seit mehr als 30 Jahren ihren Dienst tun, schafft Thomas Schink die Grundlage für ein Produkt, das die Textilindustrie grundlegend verändern könnte: Er verarbeitet Hanfstroh.
Knapp 60 Kilometer westlich forschen Wissenschaftlerinnen und Wissenschaftler im TITK – Thüringisches Institut für Textil- und Kunststoff-Forschung in Rudolstadt an nachhaltigen Lösungen für die Textilindustrie. Ein Blick auf die Klimabilanz dieser Branche reicht, um den dringenden Handlungsbedarf zu ver-stehen. Nach Angaben der Europäischen Umweltagentur (EUA) sind rund zehn Prozent der globalen CO2-Emissionen auf die Modebranche zurückzuführen. Das ist mehr, als der Flugverkehr und die Schifffahrt zusammengerechnet verursachen. Ebenso drastisch ist laut EUA der immense Wasserverbrauch von jährlich 1,5 Billionen Liter Wasser. Mitverantwortlich für diese Bilanz: die Baumwollproduktion. Für ein einziges Baumwoll-Shirt benötigt man bis zu 2700 Liter Wasser – so viel, wie ein Mensch in zweieinhalb Jahren trinkt.
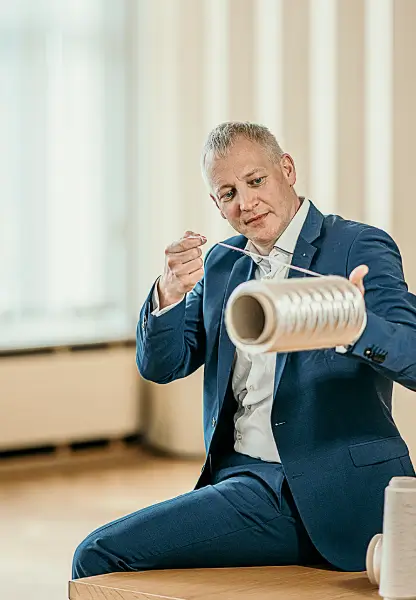
Benjamin Redlingshöfer leitet das TITK, er kennt die Heraus-forderungen der Branche. „Die Menschheit hat einen unglaublichen Textilhunger“, sagt er. Die weltweite Textilfaserproduktion hat sich in den vergangenen 20 Jahren nahezu verdoppelt. Bis 2030 ist mit einem Anstieg auf 145 Millionen Tonnen pro Jahr zu rechnen. „Das Wachstum werden wir nicht aus der Baumwolle decken können“, sagt Redlingshöfer, denn deren Produktion „stagniert schon seit Jahren“. Kein Wunder – die Arbeitsbedingungen auf den Plantagen sind oft schlecht und die Umweltauswirkungen verheerend.
Auf lange Sicht braucht es einen Ersatz für die Baumwolle, erklärt Redlingshöfer, da Kleidung in der Regel aus einer Mischung aus natürlichen und synthetischen Fasern besteht. Letztere, zum Beispiel Polyester, sind wasserabweisend, während natürliche Fasern gut Feuchtigkeit aufnehmen können. Die Mischung beider sorgt für ein angenehmes Tragegefühl. „Es bleiben die Zellulosefasern“, sagt Redlingshöfer. „Hier können wir wählen zwischen Viskose, bei deren Produktion viel toxische Chemie zum Einsatz kommt, oder der kreislauffähigen Lyocell-Faser.“
Lyocellfasern aus Hanf können die Baumwolle ablösen
Zellulose für Lyocellfasern gewinnt man herkömmlicherweise aus Bäumen. „Wir haben uns gefragt, ob es nicht eine ökologisch und ökonomisch effizientere Rohstoffquelle gäbe“, erzählt Redlingshöfer. Und hier kommt Thomas Schinks Betrieb wie-der ins Spiel. 2016 hat das TITK in Kooperation mit der Pahren Agrar erste Versuche mit Hanfpflanzen gemacht.
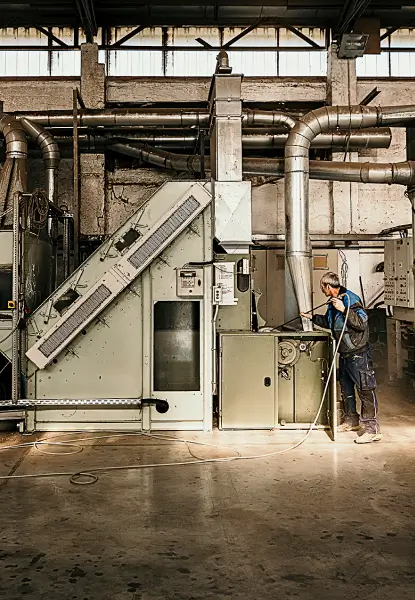
Hanf ist innerhalb von 100 Tagen erntereif, man könnte ihn zwei- bis dreimal jährlich pflanzen. Er wächst deutlich schneller als ein Baum und ist deutlich nachhaltiger als Baumwolle, denn Hanf braucht keine Bewässerung und ist sehr robust gegenüber Schädlingen, sodass keine Pestizide nötig sind. Ganz automatisch verbessert er durch sein Wurzelwerk den Boden.
Also experimentierten die Forscher im TITK in den vergangenen Jahren so lange, bis es gelang, den bisher holzbasierten Ausgangszellstoff aus Hanf zu gewinnen: Mit Lyohemp entwickelten sie eine vollumfänglich recycelbare Textilfaser, die höchsten Qualitätsansprüchen genügt. „Der zugrunde liegende Lyocell-Prozess ist die nachhaltige Technologie in der Textilwirtschaft“, sagt Redlingshöfer. „Damit können wir im anspruchs-vollen Bekleidungsmarkt eine ernsthafte Alternative zur Baum-wolle bieten.“
Darüber hinaus ist es den Forschern gelungen, die Fasern zu funktionalisieren. Bei einer gängigen Regenjacke ist die Oberfläche beschichtet, das Wasser perlt ab. Spätestens nach fünf Waschgängen sei dieser Effekt aber dahin. Ein großer Vorteil der am TITK hergestellten Funktionsfaser ist, so Redlingshöfer, dass die Funktionskomponenten direkt in die Faser eingearbeitet werden. Besonders interessant sei das für die Hautpflege, erklärt er am Beispiel eines Handtuchs. Hier wurde Vitamin E in die Faser gegeben, die Funktion ist waschpermanent. Auch nach mehr als 100 Waschzyklen ist der Effekt noch stabil, ver-spricht der Institutsdirektor, und man fühle sich nach dem Ab-trocknen wie frisch eingecremt.
Die gesamte Lieferkette in der Region aufbauen
Noch wichtiger ist Redlingshöfer aber der Umweltschutz. Wer es damit ernst meine, müsse die gesamte Lieferkette der Textilien betrachten. „Unser Verfahren bietet das Potenzial, das komplette Set-up zu regionalisieren.“ So könnten in Thüringen stillgelegte Tagebauflächen durch Hanfplantagen renaturiert werden, neue Arbeitsplätze entstünden und strukturschwache Räume würden wiederbelebt.
Im ersten Schritt bräuchte es mehr Betriebe wie den von Thomas Schink, der jährlich 700 Tonnen Stroh verarbeitet. Bundes-weit gibt es nur vier Unternehmen, die das Hanfstroh für die Textilindustrie mithilfe von speziellen Anlagen aufschließen, sprich die Fasern von den holzigen Bestandteilen trennen und reinigen. „Dort, wo andere mit einem Rollsystem arbeiten, setzen wir auf eine Hammermühle“, erklärt Schink die Besonderheit in seiner Fertigungsanlage. „Mehrere Hämmer trennen durch Schläge die Fasern vom Stängel. Das Ergebnis sind sehr saubere Fasern.“ Die Qualität seiner Hanffasern hebt sich vom restlichen Markt ab – der durchschnittliche Schäbenanteil von rund fünf Prozent sinkt auf zwei Prozent. Zudem läuft die ge-samte Produktion dank einer Solaranlage auf dem Dach der Produktionsanlage CO2-neutral. Wie zum Beweis gleitet selbst der E-Gabelstapler lautlos durch die Halle.
Thomas Schink blickt optimistisch in die Zukunft. Er emp-fängt regelmäßig interessierte Landwirte, um ihnen seinen Erfahrungsschatz weiterzugeben. „Es sind Generationen an Wissen verloren gegangen“, sagt er. Denn nach dem Anbauverbot, das bis 1996 galt, findet Nutzhanf nur sehr langsam wieder zurück auf Deutschlands Ackerflächen. Zehn Jahre nach der Legalisierung bauten lediglich rund 200 Betriebe Nutzhanf an, heute sind es etwa 850. „Schön wäre, wenn wir als Firmen dann auch miteinander kooperieren“, sagt er. „So könnten wir gemeinsam Hanffasern im großen Stil anbieten.“ Denn aktuell übersteigt die Nachfrage laut Schink die Produktionskapazitäten.
Dasselbe gilt für die Nachfolgeindustrie: Es fehlt noch an Firmen, die Hanfzellstoff zu Lyohemp-Fasern verarbeiten. Die Frage ist, wer sich in diesem Markt etabliert, so Redlingshöfer, der sich als Mittler zwischen universitärer Grundlagenforschung und Wirtschaft versteht. Der aktuell noch ungedeckte Marktbedarf biete sehr gute Voraussetzungen, um zu investieren. „In fünf bis zehn Jahren werden die Kuchenstücke verteilt sein.“ Als Technologielieferant unterstützte das TITK bereits den Bau einer Produktionsanlage in Finnland. Mit Interessenten in Frankreich und Portugal ist das Institut in Gesprächen. Und in Deutschland? „In Thüringen ist das Know-how, wir haben die entsprechenden Ingenieure – beste Ausgangslage“, sagt Redlingshöfer. „Ich bin unverbesserlicher Optimist und sicher, dass auch hier bald gebaut wird.“
Ganzheitliches Textilrecycling
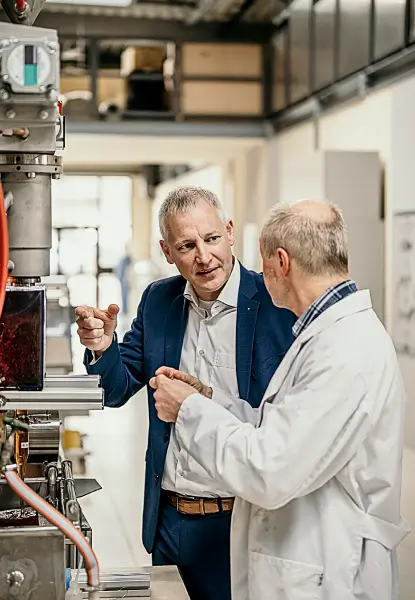
Dazu steige mit der EU-Textilverordnung der Druck auf die Textilindustrie enorm. „Wir müssen lernen, mit Alttextilien umzugehen“, fordert Redlingshöfer. „In unserer Überflussgesellschaft werden 20 bis 30 Prozent der Kleidung nie getragen.“ Durchschnittlich elf Kilo pro Europäer landen der Europäischen Umweltagentur zufolge jährlich auf Deponien oder werden verbrannt. Laut Verordnung müssen bis 2030 alle Textilien recyclingfähig sein.
Die natürliche Lyohemp-Faser – von Haus aus wiederverwendbar – wird in Bekleidungstextilien in den allermeisten Fällen in Kombination mit Polyester vorkommen. Deshalb ist es laut Benjamin Redlingshöfer elementar, ein praxistaugliches ganzheitliches Textilrecycling zu entwickeln. Hierzu soll das Demonstrations- und Innovationszentrum für Textile Kreislaufwirtschaft (DICE) am TITK entstehen. „Innerhalb kürzester Zeit haben uns über 60 Unternehmen, darunter Adidas, Vaude und Head, ihre Unterstützung für das Projekt zugesagt“, sagt Redlingshöfer und freut sich über den großen Erfolg. „Das Interesse ist bahnbrechend, wir haben massiven Forschungsdruck.“ Jetzt müssen die Forscherinnen und Forscher am TITK nur noch das tun, was sie am besten können: aus Ideen Innovationen machen.
Textil- und Kunststoff-Forschung unter einem Dach
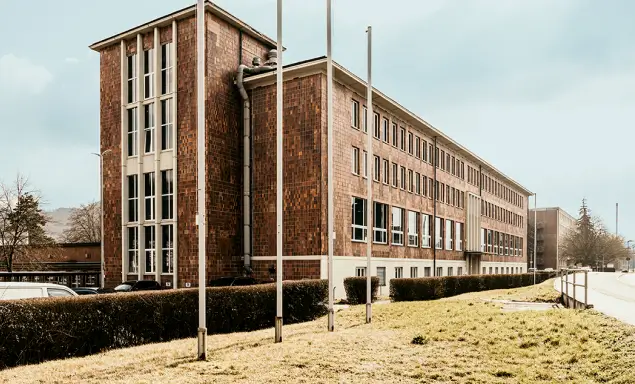
Das TITK – Thüringisches Institut für Textil- und Kunst-stoff-Forschung in Rudolstadt ist eine gemeinnützige, nicht grundfinanzierte wirtschaftsnahe Forschungseinrichtung. Die Wissenschaftler nehmen vielversprechende Ergebnisse aus der universitären Grundlagenforschung auf und entwickeln diese für die industrielle Anwendung weiter, um sie bestmöglich in marktfähige Produkte und Verfahren zu überführen. Wie vielfältig die Projekte des Instituts sind, zeigt eine kürzlich prämierte Innovation: Mit ihrem Schmelzklebstoff Caremelt entwickelte das Team eine Alternative zu erdölbasierten Klebern, die voll-ständig biobasiert und biologisch abbaubar ist.